What is a PMA Part?
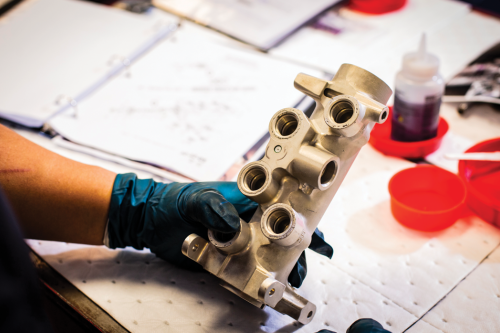
PMA parts offer several distinct advantages for airlines and MRO providers as opposed to OEMs while remaining functionally identical.
In the aviation industry, maintaining an aircraft is an expensive and critical task. In recent years, the use of Original Equipment Manufacturer (OEM) parts versus Parts Manufacturer Approval (PMA) parts has been an ongoing debate amongst aircraft owners who seek MRO (Maintenance, Repair, and Overhaul) services. While OEM parts have historically dominated the industry, PMA parts are becoming increasingly desired for MRO solutions due to their cost-saving abilities and uncompromised quality compared to OEMs. This is especially important during a time in which global travel demand is booming post covid. Currently, PMA part sales are estimated to make up less than 2% of the total spend on aircraft maintenance.
PMA parts are aircraft parts which are designed to be functionally equivalent alternatives to OEM parts, offering compatibility and performance that meets or exceeds the original specifications. Since they are not made by the original manufacturer, PMA parts go through a rigorous reverse engineering and approval process that ensures they meet the exact same safety, performance, and quality standards that are set for OEM parts. This approval process is overseen by the Federal Aviation Agency (FAA). In this approval process, PMA companies such as Jet Parts Engineering provide evidence to the FAA that their replacement parts meet all of the required regulations and that they have a system in place to ensure that future production quality is maintained. Once approved, these PMA parts can then be distributed to airlines and MRO providers. All approved parts are gathered in the FAA PMA database (called the Dynamic Regulatory System), which can be found on their website by following this link. This PMA database features over 1,500,000 current and historical PMA parts which allows the user to filter by various categories such as part number, PMA holder name, part name, make, and more.
Although FAA PMA parts fit and function in the same way as OEM parts, they offer several distinct advantages for airlines and MRO providers. As mentioned earlier, one of these advantages is reduced cost. It is estimated that maintenance accounts for around 5-15% of an airline’s total operating cost, making cost reduction a significant benefit of using PMA parts. While this was traditionally the biggest driver of PMA conversions, PMA parts have more recently been sought out to address supply chain delays. The aviation industry relies heavily on the timely availability of parts and components; OEM providers, however, have struggled to keep up due to the recent supply chain issues that have increased since the pandemic. PMA providers can capitalize on this, as they are typically more flexible when it comes to supply chain management. OEM supply is often more limited, so customers in need of MRO services turn to trustworthy PMA providers like Jet Parts Engineering. This helps make the repair process run as smoothly as possible. Since PMA parts are cheaper and more readily available, there is a common misunderstanding in the industry that these parts are “knockoffs” and are therefore lower in quality when compared to OEM parts. This could not be further from the truth, as PMAs are held to the exact same FAA regulations and standards as OEMs. The differences in performance are indistinguishable. The utilization of FAA PMA parts enables customers to navigate supply chain challenges resulting in more efficient aircraft maintenance operations, all at a discounted price.
Jet Parts Engineering (JPE), a Seattle based company which was founded in 1994, is one of the leading PMA part suppliers in the industry. The company has over 1,400 PMA parts in its catalog available for purchase, all of which have been meticulously reverse engineered and have received airworthiness certifications from the FAA. In addition to an extensive catalog, JPE also partners with airlines and MROs who need a replacement part that is not part of their current inventory. Due to the company’s strong affiliation with the FAA, JPE can develop and certify these parts more efficiently. Jet Parts Engineering understands the challenges faced by customers in the aviation industry, particularly in terms of cost management and the timely availability of parts. This is why the company was founded under the principles of making aircraft maintenance more affordable and working in conjunction with customers to fulfill their requests. The team at Jet Parts Engineering is filled with some of the brightest minds in the industry who have extensive experience with parts and repairs in most aircraft systems from nose-to-tail and have developed a strong reputation for delivering exceptional products with unbeatable service.
The engineers at JPE consistently strive to exceed industry standards delivering top quality parts that often surpass those produced by OEMs. They carry expertise in various disciplines such as 3D CAD design, laboratory testing, metallurgy, and advanced manufacturing technologies. With a commitment to innovation, the team is continually evolving to incorporate the latest materials, processes, and manufacturing techniques. The company’s extensive product line features a wide variety of PMA parts that cover a full range of ATA chapters - including pneumatics, avionics, hydraulics, fuel, oil, electrical, and more. JPE supplies components that fit various systems and structures, including pumps, generators, valves, actuators, engines, thrust reversers, engine cowls, APU's, airframes, control surfaces, landing gears, etc. Their wide range of parts cater to commercial aircraft from smaller regional jets to super jumbos like the A380 and B747.
The company prioritizes making the purchasing process as easy as possible for its customers. By providing an easy-to-use ecommerce portal found on the website, customers are given immediate access to pricing, availability, and technical information of the desired FAA PMA parts, while enjoying the convenience of effortless order placement and tracking. Furthermore, JPE puts a strong emphasis on customer service, ensuring all orders of parts in stock are provided within 3 days. This quick turnaround time allows airlines and MRO providers to minimize downtime and efficiently carry out necessary maintenance and repairs.
There are several notable trends that consumers can expect to see in the future of the MRO industry. It is expected that the annual growth rate of the PMA market will continue in double-digits, exceeding that of the MRO market. The increased acceptance of FAA PMA parts by airlines helps ensure a competitive market by preventing OEMs from monopolizing and price gouging the industry. However, despite the progress, there are still factors limiting full widespread acceptance. One major challenge is that aircraft financiers often restrict aircraft operators from using PMA parts due to concern that they might reduce the resell value of the aircraft. Additionally, there are still outdated perceptions associated with PMA parts regarding false narratives of lesser quality, support, and warranty coverage. These misconceptions prevent potential airlines from realizing the benefits of availability and reduced maintenance costs that PMA parts offer.
As the PMA market continues to grow, Jet Parts Engineering is ready to help. With its experienced team, innovative problem solving, and high-quality parts, JPE is committed to making aircraft maintenance more affordable and efficient for its clients worldwide. While there are some factors that limit total acceptance, Jet Parts Engineering continuously disproves misconceptions regarding differential quality between OEM and PMA parts. As airlines and MRO providers look to navigate the ever-evolving landscape of aircraft maintenance, Jet Parts Engineering stands out as a leading PMA part provider in the industry.